At a Glance
- Warehouses are critical to global trade, not only as storage hubs, but also in optimising supply chains, stabilising prices, and adapting to changing market demands.
- Warehouse management is more importance than ever for customer satisfaction and profitability. Best practices include data-driven optimisation, employee training, and automation.
- Change management expertise enables your people and organisation to embrace new technologies and achieve best-in-class warehouse management benchmarks.
Modern warehouses are no longer just storage spaces; they are vital cogs in the machinery of global trade. This booming industry is expected to reach US$605.6 billion by 2027, with a compound annual growth rate (CAGR) of 4.9% between 2022 and 2027.Â
Warehouses are the cradle of raw materials and the repository for semi-finished and finished goods. They also facilitate the efficient distribution of goods during seasonal fluctuations or turbulent times and help to stabilise prices by holding inventory in times of scarcity to prevent market dissonance. Â
In recent years, companies have realised the potential of the warehouse by centralising production and storage facilities to organise a more efficient flow. This strategic manoeuvre has expanded the role of the warehouse, transforming it into a distribution hub for a wider, more demanding global audience.  Â
Industry players have also shifted gears since 2020 as a result of rapid changes in customer demands and supply bottlenecks and have had to adapt to receiving changing items and increasing shifts in needs. During the same period, online groceries and e-commerce have seen a surge in demand due to COVID-19-related movement restrictions. Â
These changing needs have led to complicated internal logistics processes to meet the demands of an increasingly complex market. As a result, managing complex warehouses effectively and efficiently has become a challenging task.  Â
The importance of warehouse management to modern businessÂ
Efficient warehouse management is critical because smooth warehouse operations are key to cost-effective, efficient supply chains. They ensure a seamless flow of products, eliminating costly delays and stock-outs. Â
But it should be noted that warehouse management is more than just preventing hiccups. It plays a role in customer satisfaction. For example, poor warehouse management for an e-commerce platform can lead to order fulfilment issues such as incorrect orders or late deliveries, resulting in negative online reviews and increased churn as customers switch to competitors. Overall, poor customer satisfaction leads to lost sales and lower profitability.Â
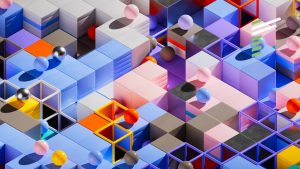
Realigning Structure and Processes: Why organisation design matters
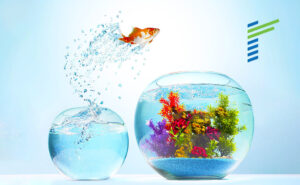
Effective change management: Questions to ask
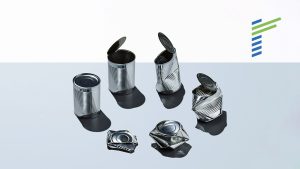
Manufacturing: Does your supply chain need a makeover?
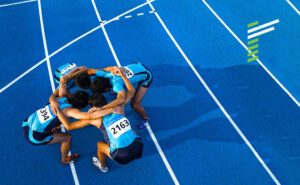
Winning business strategies from the world of sports
Ready for a change in your organisation?
Warehouse best practices
A supply chain is only as strong as its weakest link. Therefore, making excellent warehouse management a top priority is essential. Here are some warehouse best practices:
1. ABC classification of materials
Implement ABC classification by segmenting your facility into zones according to pick types. This will streamline both picking and replenishment processes by grouping similar items with comparable storage and picking methods. For example, you can designate zones for high-volume items, low-volume items, and special items that require unique handling or storage.
2. Capture real-time, actionable data
The Internet of Things (IoT) can give you complete visibility into your warehouse. By using a warehouse management system (WMS) that integrates sensors into all aspects of your warehouse operations, including inventory management and picking times, you can identify gaps and weaknesses in your warehouse system. You can use the data to target these areas for improvement to make effective changes.
3. Implement automation judiciously
With advances in artificial intelligence (AI) and automation, it is important to proceed with caution. While automation proves efficient in numerous scenarios, it is not always optimal. Understand and assess the return on investment (ROI) before committing to automation equipment. If the savings can be quickly recouped, then investment in equipment such as automated guided vehicles, robotic picking, and automated sorting system is likely to be justified. However, if the payback period is long, it may be wiser to allocate funds to more beneficial areas.
4. Focus on replenishment
Replenishing inventory should be as easy as picking it. When designing the warehouse, the ABC zones should include ease of replenishment as well as picking. The WMS should trigger replenishment when inventory levels fall below a pre-defined threshold. This will prevent out-of-stocks and ensure there is sufficient stock to meet demand. 
5. Train relentlessly
It is not enough to simply reorganise the warehouse and implement a new WMS. For change to be effective, employees must embrace the new system. Fortunately, times of change provide opportune moments to instil good habits. Habits consist of a cue, a routine, and a reward. Incorporating all three into a training programme will help break bad habits and establish good ones.
Document the training sessions provided and ensure that comprehensive training programmes are extended to new employees, with regular refresher sessions as part of the ongoing training strategy.
Defining best-in-class warehouse management
The benchmarks for warehouse management excellence revolve around four key areas:
- Organisation: Everyone involved is cross trained on a variety of tasks and equipment.
- Knowledge: There is a comprehensive view of order status, inventory levels, and labour allocation across the company. This real-time knowledge enables decision-makers to respond quickly to fluctuations in demand and streamline overall operations.
- Technology: The use of advanced technology is a cornerstone of best-in-class warehouse management. This includes a WMS enhanced with labour management tools, slotting technology, and other innovations.
- Performance metrics: Exceptional warehouse management will have your key performance indicators (KPIs) demonstrating 97% on-time and complete shipments, 99% picking accuracy; one day or less from order receipt to warehouse shipment, and two hours or less dock-to-stock cycle time.
Using these benchmarks, where does your warehouse performance stand in relation to industry standards? Understanding whether you are a laggard, an average performer, or an industry leader is critical to developing strategies to take your warehouse management to the next level.
Why expert help matters for raising warehouse management standards
The competitive landscape is fierce, so warehouse excellence is no longer optional. To stay ahead, warehouse operators should apply these best practices and benchmarks for warehouse management excellence to their specific operations and invest in the appropriate technologies and strategies.
It is also important to keep abreast of the latest developments in the field to remain agile and responsive to changing market dynamics. It should be noted that even the most exceptional strategies will fall flat without buy-in from the team.
This is where expert help matters. With over 25 years of experience in change management, Renoir focuses on achieving results through behavioural change, empowering your people to embrace change, adopt new technologies, and drive success. We focus on strategies, tools, and people – the factors that deliver lasting results.
Looking for a change management consulting firm to unlock the full potential of your warehouse operations?