At a Glance
- Maintenance planning plays a significant role in improving the longevity and efficiency of physical systems or equipment.
- A key catalyst for a robust maintenance planning approach is the reduction of breakdown risks, which in turn, leads to a reduction in the length of downtime and the avoidance of plant closures due to unforeseen equipment failure.
- Renoir was once engaged by a leading manufacturer of foundry products to improve its operational efficiency where we successfully reduced maintenance downtime by 38%.
We have all heard expressions that describe how things in life require careful thought and preparation, and that it is best to take precautions. A great saying that best sums up this sentiment is, “An ounce of prevention is worth a pound of cure”.
This wisdom from Benjamin Franklin serves as a reminder that investing time and effort upfront can save you from bigger problems down the road. In essence, it is better to take preventative measures than to suffer the consequences later on.
Maintenance, in the context of this principle, refers to activities that maintain and safeguard equipment and systems, or restore them to a condition in which they can perform their required functions. Maintenance planning, the ability to identify the right objectives and tasks for preventive maintenance, is important because it ensures that adequate resources are available when repairs are needed.
In this article, we look at the importance of maintenance planning in an organisation, and how to create or update a maintenance plan.
Why you need maintenance planning
Maintenance planning plays a significant role in improving the longevity and efficiency of physical systems or equipment. Priority-based planning of maintenance activities can increase productivity by at least 5%, at least according to one automotive case study.
A key catalyst for a robust maintenance planning approach is the reduction of breakdown risks, which in turn, leads to a reduction in the length of downtime and the avoidance of plant closures due to unforeseen equipment failure. This helps to increase productivity and revenue, while maintaining positive relationships with suppliers and customers.
In addition, addressing maintenance planning deficiencies improves the accuracy of planning processes, procedures, resource allocation, and performance management, ultimately promoting a safety culture. Regular reviewing and updating a maintenance plan is, therefore an integral part of an effective safety policy.
How to maintain or update your maintenance plan
Maintaining the effectiveness of your maintenance plan requires ongoing attention and adjustments. Here are some critical aspects (non-exhaustive list) to consider:
Job libraries. Each routine preventive and condition-based maintenance task should be accompanied by a clear set of work instructions, including safety guidelines and established standards. These standards may include unit rates for subcontracted work, crew size, and required skills such as electrical, mechanical, instrumentation, and scaffolding expertise. For non-routine tasks, construction production rates such as hours per metre of cable laid may occasionally be used. If standards are not available, the duration of the maintenance is at the discretion of the technicians involved.
Materials ordering. Getting the right materials is an important part of maintenance planning. Each piece of equipment should have a list of materials, commonly referred to as a Bill of Materials (BOM). This BOM is a valuable resource for quickly identifying the components required for maintenance tasks.
Another important tool is a repository known as a Material Master. In this repository, companies must diligently maintain essential information such as supplier information, delivery schedules, and agreed prices. This helps to avoid overpaying for materials, labour, and other costs. When ordering materials, categorise them as ‘stock’, ‘non-stock’, or ‘critical spares’ in the Material Master to facilitate tracking and ensure that procurement is synchronised with the need to avoid supply chain disruptions.
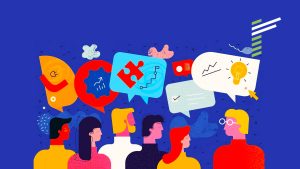
DILO: Driving behavioural change and improving productivity
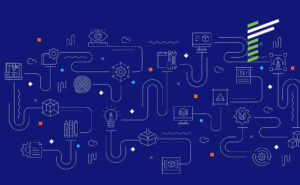
How OEE can help improve your manufacturing operations
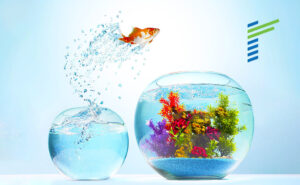
Effective change management: Questions to ask
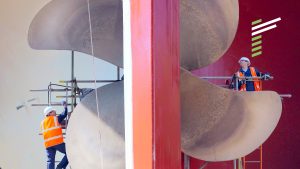
Ready for a change in your organisation?
Job prioritisation using a Risk Assessment Matrix (RAM)
Not all jobs are created equal in terms of importance. The Risk Assessment Matrix (RAM) is used to assess the potential risks associated with different tasks, ranging from massive loss of production, quality, assets, health and safety, and the environment to none.
The RAM assigns a score to each job based on the level of risk associated with it. The score guides scheduling decisions, determining whether a particular job should be addressed immediately or deferred to a later date. The score also provides insight into the effectiveness of an organisation’s Reliability-Centred Maintenance (RCM) process.
Plan A Day Advanced (PADA)
The final stage of the planning process involves supervisors and/or technicians meeting at the end of the day to ensure that all necessary preparations are in place for the tasks scheduled for the following day. This may include organising materials and tools, securing work instructions, preparing job safety analyses, and finalising drawings. The primary objective is to ensure that when they arrive the next morning, everything is in place to get straight to work and optimise productivity.
Planning is easy, execution is hard
Often the most challenging aspect of maintenance planning is getting people to follow procedures and excel at record-keeping, which is entirely a behavioural problem.
People are the key. Renoir can support your journey to operational excellence by changing mindsets and behaviours that can facilitate, among other things, the implementation of procedure compliance.
Are you ready to change the behaviour of your employees to improve maintenance compliance?