At a Glance
- Overall Resource Effectiveness (ORE) refers to the level of effectiveness in the use of all our resources, equipment, operators, technicians, site management and support systems.
- It is a useful tool for decision-makers to conduct in-depth analysis and continually improve the performance of available resources.
- Using ORE can help equipment-dependent organisations improve resource utilisation and throughput.
In the high tech and manufacturing industries, which are heavily reliant on finance and equipment, the ability to remain competitive depends on the efficient allocation of capital and labour. Â
Much of the focus in these industries is on forecasting demand, strategically planning the use of equipment, and properly managing orders to maximise the use of available resources. However, not enough attention is given to resource management. Â
This article discusses Overall Resource Effectiveness (ORE) as a strategy for improving resource management, which can be a useful concept for increasing overall productivity and resource efficiency. Â
What is ORE?Â
Overall Resource Effectiveness (ORE) can be defined as the level of effectiveness in the use of all our resources, equipment, operators, technicians, site management and support systems. It is an extension of the more familiar concept of Overall Equipment Effectiveness (OEE). Â
While OEE is often used in manufacturing, it is less comprehensive than ORE. In essence, OEE focuses on three variables, which are availability, performance, and quality, whereas ORE has seven variables, namely:Â Â Â
- ReadinessÂ
- PerformanceÂ
- QualityÂ
- Availability of facilityÂ
- Changeover efficiencyÂ
- Availability of materialÂ
- Availability of manpowerÂ
These variables are measured to produce an overall ORE score, where the maximum score is 100%.Â
The OEE factors do not provide a clear measure of the losses incurred during planned production time, which is an area for improvement. Conversely, ORE, through its readiness variable, accounts for losses during planned production time. In addition, OEE provides an overview of machine uptime, while ORE looks at the whole plant, including machines, tools, jigs and fixtures, and gauges and instruments. Â
A case study of a manufacturing company found that the overall effectiveness score using OEE was 56.44% (out of 100%). When using the ORE measure, the company found that the overall effectiveness was 53.02%. This nuanced metric, ORE provides greater insight into production losses, revealing more room for operational efficiency. With this insight, companies gain a more comprehensive understanding of how all resources are being used.Â
In a broader context, ORE serves as a useful tool for decision-makers, providing them with the means to conduct in-depth analysis and continually improve the performance of available resources. ORE can also be used to assess the current state of the manufacturing system and provides a robust platform for benchmarking effectiveness within the industry.Â
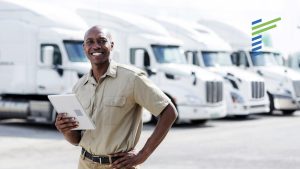
How to improve fleet efficiency for operational excellence
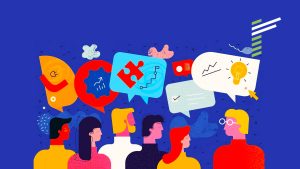
DILO: Driving behavioural change and improving productivity
Ready for a change in your organisation?
Benefits of ORE
Using ORE can bring many benefits to equipment-dependent organisations. Two primary benefits associated with implementing ORE are:
- Improved resource utilisation. The adoption of ORE methodologies results in improved efficiency in terms of flow time and cycle time. Reducing cycle time by half can double the performance and capacity of operations.
- Improved throughput. Increased resource utilisation also contributes to throughput, or the amount of material passing through the operation. Improved throughput means more and faster output, which helps organisations accelerate the pace of achieving organisational production targets.
How to practice ORE
To practice effective ORE management, you need to apply the management principles of both OEE and ORE. These include:
1. Improving sales and facility loading. The basis of ORE management is to ensure that the plants are fully loaded, meaning they operate at their maximum capacity. This involves optimising the use of existing resources and driving sales to maintain and meet demand for these resources.
2. Improving availability and utilisation. Companies must strive to maximise the availability and utilisation of equipment. This requires better planning and supply chain management.
3. Improving performance and efficiency. The pursuit for higher ORE scores underlines the importance of production efficiency. This can be achieved through a variety of strategies, including debottlenecking, line balancing, and the implementation of improved control mechanisms.  
4. Improving quality management. Quality is a fundamental concept in ORE management. Maintaining high-quality standards is therefore non-negotiable. One area of focus for quality improvement is manual labour, as there is a correlation between quality and human behaviour. 
Leave ORE to the experts
Many manufacturing companies struggle to understand and implement ORE, OEE, and OLE (Overall Labour Effectiveness). These concepts require a deep understanding of manufacturing processes and expertise in operational excellence.
As Industry 4.0 technologies create new opportunities for manufacturers to ideate, manufacture, and distribute products in innovative ways, this progress comes with enormous pressure and urgency to improve asset realisation, manage inventory levels, improve resource productivity, and manage multi-SKU portfolios, while meeting customer demands and delivery commitments.
Renoir consultants and subject matter experts can help your organisation develop an implementation roadmap to make fundamental changes in the way you do business to keep pace with market changes. Whether it is resources, labour or equipment, we can help you design and implement a fit-for-purpose organisational structure that can transform your operations.
Please assess my team and organisation to start building a roadmap.