At a Glance
Renoir worked with a healthcare centre to tackle high supply costs. With better supply chain management, results seen were significant:
- Stock was reduced by 36%
- A 33-40% increase in inventory turns
- 98% (all-time high) order fill rate
- Creation of a new core culture
Background
With over 900 licensed acute care beds, this client is a teaching hospital that serves as a main hospital facility in Pennsylvania. It has been established as a leader in neurosurgery, gastroenterology, orthopedics, urology and geriatrics.
The Challenge
Faced with a spiraling supply cost per case, the President and Chief Executive of a hospital in Pennsylvania decided to engage the Renoir Corporation. Renoir carried out a three-week survey of the supply chain on two of its sites to understand the issues within the inventory control and distribution systems.
What We Did
After an initial analysis, it was felt that the client would not benefit sufficiently from a project but instead, a more comprehensive program for its main site. The proposal identified improvement opportunities in:
- Balance sheet inventories.
- Point of care inventories.
- Pharmacy inventories.
- Operating room (OR) inventories.
A review of the existing management information system (MIS) was also recommended.
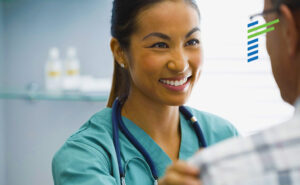
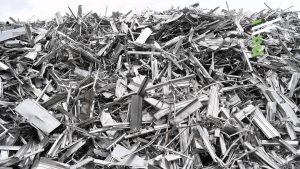
Removing Supply Chain Inefficiencies for Enhanced Performance
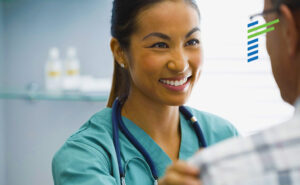
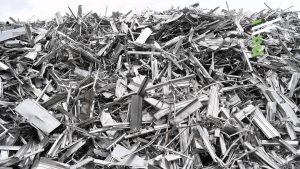
Removing Supply Chain Inefficiencies for Enhanced Performance
Cost savings with better performance and supply chain management.
The selection and training of a Task Force comprising members of the client’s management team was a key step in getting buy-in and ownership throughout the hospital. Results from specific areas included:
Balance Sheet Inventories
- A 36% reduction
- A 33% increase in stock turns
- A 98% all-time high order fill rate
Point of care (POC) inventories
Borrowing from the manufacturing sector and developed with the nurses, a KanBan system was installed to reduce and make more accurate point-of-care inventories, the results of which prompted a physician to say: “There should be a picture on the wall of whoever has come up with this idea!”
Pharmacy
Measurable effects were:
- 33% reduction in inventory.
- 40% increase in stock turns.
Operating Rooms
The ambitious aim of standardising and reducing general medical and surgical supply stocking points was achieved with no adverse effect on patients. Operating room staff readily took on responsibility and accountability for managing supplies through a highly consultative approach, a big change from previous consulting assignments. As a Supply Technician in the Operating Room explained, “This project has completely changed the hospital’s attitude to consultants.”
The Results
Project stakeholders were unanimous in their agreement that the project had delivered beyond its original promise. Sustainable operational improvements from the project include:
- Implementation of improved processes to optimise supply chain management for the long term.
- Implementation of new Management Control Systems to monitor processes, maintain compliance and continue improvements.
- Creation of a core culture that understands the importance of managing the supply chain in hospital operations and acts accordingly.
- Development of taskforce members to carry on and expand supply chain optimisation efforts after project completion
“I am very impressed with what we have been able to accomplish with the dedicated assistance of Renoir. They have delivered on all the commitments they made in developing the project schedule – often ahead of schedule – and turned around even those most skeptical about the ability of consultants to provide added value.”
CEO
Improve hospital inventory management for cost savings.