At a Glance
- A leading pharmaceutical company faced challenges with excessive manpower costs (2x higher than best-in-class competitors) and significant operational inefficiencies.
- Renoir implemented a systematic approach to manpower optimisation and cost reduction across 21 departments.
- Achieved validated cost savings of 11% on manpower costs and 9% headcount optimisation, along with 1.1% reduction in power and energy costs.
Key results
Validated manpower cost optimisation opportunity of
11% on a base of INR 57.44 Cr. (US$ 6.6M)
Validated manpower headcount optimisation opportunity of
9% on a base of 947 headcounts
Validated Power & Energy cost reduction opportunity of
1.1% on a base of INR 62.45 Cr. (US$ 7.2M)
Background
Headquartered in Chennai, India, the company had a substantial workforce, with an initial headcount of 947 employees assessed during the project. It ranks among the top 50 pharmaceutical companies in India and operates across the entire pharmaceutical value chain—from research and development to manufacturing and marketing. The client approached Renoir to collaborate on this project aimed at reducing costs and improving productivity at their Chennai facility.
Analysis
Renoir conducted a comprehensive analysis of the organization, covering 576 employees both quantitatively and qualitatively.
This analysis uncovered several critical inefficiencies:
- Poor Management Structure: The middle management layer had the lowest span of control utilisation compared to the junior and senior management layers
- Excessive Supervision Layers: Multiple levels of supervision resulted in a lack of accountability
- Sub-optimal Workforce Allocation: High tenure employees in low grades indicated poor role fitment and career stagnation
- Activity Redundancies: Considerable overlap between the activities of unique positions and their line managers
- Cost Inefficiencies: The employee cost was twice that of best-in-class competitors
- Resource Allocation Issues: 66% of total employees worked in non-production related departments
- Utility Costs: Power and fuel costs were twice that of best-in-class competitors.
These findings highlighted the urgent need for structural reorganisation and cost optimisation to restore competitiveness.
Project Approach
Renoir divided the project into two distinct workstreams:
Manpower Productivity Stream:
Departments were divided into 6 equal sprints based on headcount.
Each sprint included:
- Validation of current organisational structure, roles, and headcount
- Detailed activity listing for each unique position
- Validation of activity listings with line managers
- Observation studies (DILO, Wrench time study, Ratio Delay)
- Work content analysis where applicable
Other Expenses Stream:
- Focused investigation of power & energy costs
- Detailed analysis of service contracts
- Buy vs. outsourcing studies for each contract
- Positional manning studies for specific contracts like security and canteen services
- Implementation of contractor pass-through savings to the client
This methodical approach ensured comprehensive coverage of all operational areas with potential for improvement.
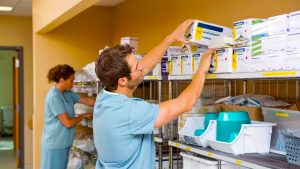
Better hospital inventory management cuts stock needs by 36%
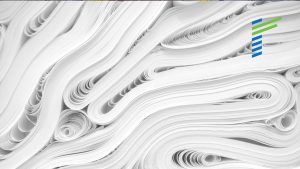
Paper mill cuts material loss by 300% with maintenance planning
Ready for a change in your organisation?
Implementation
The implementation phase involved a practical trial of the newly designed organisational structures in four key departments: Mechanical maintenance, Boiler, Key product line plants, and RM Stores. Â
This trial implementation included a detailed assessment of employees and the creation of a surplus list. Based on the assessment scores, employees were categorised to inform future decisions regarding role alignment.Â
 Renoir Consulting worked closely with the client’s teams throughout this phase, providing a scientific approach to manpower optimisation with intense studies and data backing. This collaborative approach ensured alignment among various internal teams and facilitated sign-off on the proposed changes. Renoir also focused on imparting knowledge to the client’s taskforce, aiming to develop internal capabilities for future leadership in optimisation initiatives.Â
“We had before tried to optimise our manpower, but we were not successful. Renoir has provided a scientific approach to manpower optimisation with intense studies & data backing and also aligned the various internal teams to signoff.
Their hands-on approach sets them apart from other consulting peers. They have also imparted excellent knowledge to our taskforce, who can be groomed into future leads in our organisation. We are happy with the project’s outcome and would recommend their services to similar projects.”
 – Whole-time Director
Results
The 11% reduction in manpower costs represented approximately INR 6.32 cr. (US$ 726,000) in annual savings
9% workforce optimisation opportunity enabled the client to allocate resources more effectively across departments.
1.1% reduction in power and energy costs represented approximately INR 0.69 Cr. (US$ 79,200) in annual savings .
Taskforce gained valuable skills through Renoir's approach, preparing them to become future leaders in the organisation.
Beyond the immediate financial impact, the client benefited from Renoir’s systematic approach to organisational design and workforce optimisation, which provided a sustainable foundation for future improvements.
*We have intentionally omitted client-specific details to uphold strict confidentiality.  
Learn actionable insights for your organisation's productivity transformation.