At a Glance
After a 27-week project with Renoir, the following results were achieved for the client:
- Improvement in Overall Equipment Effectiveness (OEE) of Blast Furnace Operations between 6 and 7%
- Reduction in fuel rate between 1 and 2%
- Reduction in off grade generation between 2 and 5%
- Improvement in average stability factor for 7 key parameters by between 4 and 9
Background
The client was incorporated in 1990 and produces pig iron and ductile iron (DI) pipes at its manufacturing plant in India. The plant’s annual hot metal production capacity is 500,000 tonnes out of which 200,000 tonnes, which is converted into DI pipes and 300,000 tonnes into pig iron. It is a preferred supplier to the foundry as well as water and sanitation sectors in India and across Southeast Asia and Africa by maintaining stringent industry standards and producing best-in-class products.
The Challenge
The client had experienced several unscheduled interruptions that were impacting the health of the 2 blast furnaces and disturbed the continuity of furnace operations which is key to achieving the business plans. The management wanted to manage this issue through the adoption of systems and processes to better control blast furnace operations.
Given Renoir’s long-standing association with the client, their team was aware of Renoir’s ability to work with them on the ground and help them navigate the change management journey. A two-week analysis of the blast furnace operations and maintenance teams yielded the following improvement opportunities:
- Reduce variation of process control from person to person and shift to shift
- Clarify roles and responsibilities and active supervision of shift personnel
- Adopt a data-driven approach to maintenance management
What We Did
To develop the management control systems for both operations and maintenance, the project team embarked on an 8-week long Focus Process® which was followed by the Installation phase.
Operations
The studies conducted during the Focus Process® were in 3 main areas of the blast furnace: cast house, control room and pig casting machine (PCM). The findings led the team to broadly focus on improving active supervision and short interval control for the supervisors and managers, as well as minimizing the variations in Operations.
To implement short interval controls, a robust review mechanism was installed that enabled the team to take unified decisions after thorough deliberation, supported by data. At the shift level, a composite score (called the ‘shift score’) was calculated, thereby providing an objective way of evaluating shift performance. A casting schedule was also provided and adherence monitored at regular intervals during the shift.
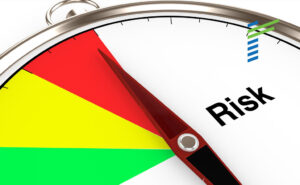
Fix it before it breaks: Maintenance planning for operational excellence
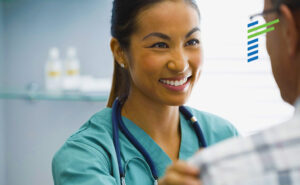
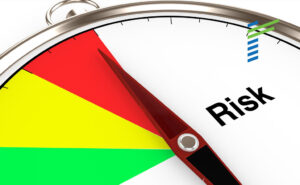
Fix it before it breaks: Maintenance planning for operational excellence
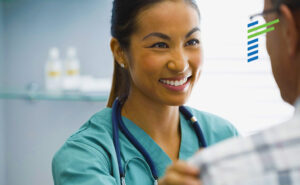
A routine was established for supervisors to visit and capture deviations in all areas under scope during his shift. Capability studies identified gaps in the technical abilities of the shift supervisors. Hence, a schedule of technical trainings was established with internal subject matter experts conducting sessions to link theory with the practical aspects of blast furnace operations.
A statistical approach was implemented to ensure that the key process parameters were maintained within specification limits. The approach was coupled with decision trees and an escalation matrix to ensure that abnormal situations were brought back under control quickly. This helped reduce variations in furnace operations while aligning the decision making across shifts.
Maintenance
The key areas of improvement identified during the Focus Process® were data management, planning and shutdown management. Data capturing mechanisms were set up early in the assignment and KPIs were agreed to evaluate the day-to-day performance of the maintenance team. An extensive exercise of equipment listing, ageing and ranking based on criticality was carried out and equipment history cards were set up to capture each event for A-ranked equipment. Dashboards were created and a review meeting structure was established to review the performance of each department (Electrical, Instrumentation and Mechanical).
A preventive maintenance (PM) schedule was installed at the start of every month and compliance monitored, initially at the department level, and later a crossfunctional team was formed for certain equipment to reduce the downtime for PM. To address the concern of spares availability, a weekly monitoring system was setup between the maintenance and procurement teams to reduce the purchase requisition to purchase order cycle time. In parallel, the critical spares were mapped and inventory levels monitored on a weekly basis.
Gantt charts were introduced to map the shutdown jobs and their dependencies, while focusing on the critical path to track progress during execution. The job-wise plan vs actual durations were analyzed post-shutdown and learnings were shared in review meetings for further improvement.
Results
The systems implemented contributed to an improved performance of the blast furnaces – both in terms of output and stability – with 13 out of 14 key process parameters operating in a more stable range compared to the baseline.
A structured approach to shift supervision and daily management ensured consistency of the results post-implementation, while the capability development program initiated will help in smooth operations in the future.
Address gaps in operations and maintenance for smoother performance.