Background
Iron ore, the second most important commodity after oil, plays a vital role in crude steel production. It is primarily used in steelmaking, serving the trillion-dollar global metal market each year.Â
There are four types of iron ore, classified according to their iron content, geological origin, and mineral composition – hematite, magnetite, limonite, and siderite. As the different types of iron ore have different iron contents, they are used in different industrial processes.
Our client is one of the world’s largest producers of hematite iron ore. They also operate a steelworks and export hematite iron ore to Asian countries.
Analysis
Following a previous successful collaboration, our client again engaged Renoir to assess its downstream operations. The analysis focused on identifying opportunities within their magnetite stream, which consisted of five plants – a crusher, an iron ore beneficiation plant (OBP), a concentrator, a filer flux plant, and an induration plant.
Our results identified several opportunities for improvement, which are:
- Improve active supervision
- Improve value-adding activities
- Address data inconsistencies
- Implement short internal control
- Improve review meetings
- Streamline root cause analysis processes
Project Approach
This project was aimed at implementing the relevant components of the Management Control System (MCS) to achieve the following benefits:
- 8% increase in throughput
- 10% reduction in overtime
- 10% reduction in contractors
Two geographically focused Management Action Teams (MATs) were formed to achieve the targeted results. Each team consisted of a MAT chair, subject matter experts, a taskforce, and a Renoir consultant. The teams were responsible for project activities, including providing regular progress reports to the Steering Committee according to a timetable.
“It would have taken us more than two years to achieve what Renoir did in less than a year. We tried other initiatives before, but not in the systematic and sustainable way that the project has brought.”
– Improvement Manager
Implementation
Management Control System
The successful delivery of the project depended on the strategic implementation of the Management Control System (MCS). This MCS ensured alignment in planning, execution, reporting, and variance analysis. A key aspect of the MCS required the integration of Short Interval Control (SIC) in both operations and maintenance to address the need for improved active supervision.
For operations, a structured daily/weekly plan was developed for team leaders, supported by SIC tools to monitor the relevant metrics every two hours. Deviations from the plan were addressed to ensure that the daily tasks execution was on track.
A similar structured day/shift approach was introduced for the maintenance team, complemented by SIC rounds and checklists to evaluate the effectiveness of routine and non-routine maintenance activities.
Contractor Expenditure
This project also reviewed contractor activities by assessing in-house capabilities to deliver activities, with or without training. In addition, a contractor management tool was developed and installed to improve both the planning and execution of activities by external service providers.
Overtime Spend
A comprehensive overtime system and process was implemented to track the planning and use of overtime. This system enabled control across various operational aspects, resulting in enhanced efficiency.
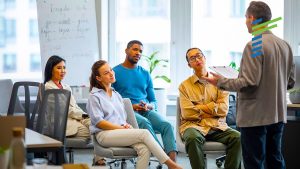
Understanding on-the-job coaching for performance breakthrough
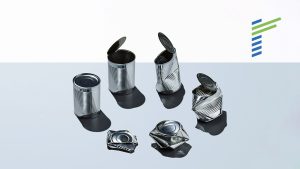
Manufacturing: Does your supply chain need a makeover?
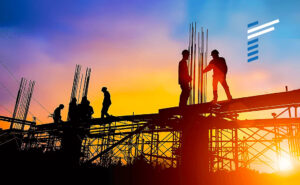
4 actions to drive operational excellence in construction

Maintenance Excellence: How to go from good to great
Ready for a change in your organisation?
Results
The primary objective of this project was to establish the MCS to maintain and improve the return on investment (ROI) through gains made in throughput and cost savings. This was achieved through accurate metric measurement and robust review mechanisms.
ROI exceeded target from 3:1 to 15:1
Throughput increased by 9%
Contractor expenditure was reduced by 7%
Overtime spend was reduced by 43%
*We have intentionally omitted client-specific details to uphold strict confidentiality.  
Need help redesigning your business processes and systems to achieve your business goals?