At a Glance
- A large, vertically integrated energy company, active in all aspects of the oil and gas industry, was struggling to implement new ways of working as most of its work was carried out remotely in offshore locations.
- Renoir carried out a brief analysis, identified a number of issues and opportunities, and began a 10-month project to address the key challenges facing the company’s management.
- The project provided the company with the necessary structure, tools and skills and led to a step change in the organisation’s operational approach, resulting in faster problem resolution and improved financial performance.
Key results
Reduced backlog by
70%
Reduced engineering workload and labour costs by
US$1.4 million
Increased the rate of planner-generated corrective task lists by
212%
Savings during the project year
US$7 million
Background
Our client is a major vertically integrated energy company operating in all aspects of the oil and gas industry. This includes exploration and production, liquefied natural gas (LNG), refining, petrochemicals, power generation, distribution and marketing.
It also has significant operations in many other areas of the world, with upstream production covering both conventional and unconventional oil and gas. The company has also invested heavily in renewable energy as part of its initiatives to broaden its energy portfolio and reduce its dependence on hydrocarbons.
The Challenge
Our client was struggling to implement new ways of working because most of its work was carried out remotely in offshore locations. They were using outdated tools, meeting structures, and manual daily reports and objectives, resulting in confusion, missed targets and a lack of workforce efficiency.
Renoir had previously completed projects with the client in various other geographies and businesses with great success in this area. These projects included institutionalising ways of working with front-line staff using digital tools. We also have experience of delivering remote site management systems across many industries with sustainable results.
Analysis
Renoir conducted a brief analysis and identified the following issues and opportunities:
Current Issues
- System control: The current system dictates the workflow rather than empowering the people using the system to manage and control it.
- Digital workplace: A move to a digital workplace is needed to improve work alignment, seamless handovers, and focus efforts on value-added work.
- Planning bottlenecks: Several factors contribute to planning delays – clustered due dates, potential resource imbalances, inaccurate data in maintenance build and materials, system and tool limitations, and planner limitations. There is a need to create technician/planner roles for routine tasks during high volume periods.
- Inflated planning hours: There is an opportunity to accelerate the feedback loop (CI) and implement estimating tools and guides for greater hour accuracy prior to plan release.
Â
Work Management
- Engineering integration: Poor adherence to engineering practices. Interfaces between engineering and work management need to be improved.
- Activity integration: Activity integration is followed but not yet effective. Functional readiness assurance lacks appropriate guidelines, enforcement and accountability.
Â
Collaboration and Resource Management
- Priority alignment: Further alignment between sites and functions is needed, especially in programme execution.
- Resource Control: Programme implementation lacks effective methods for allocating resources and managing third party resources on-site. Performance management for contractors is also hampered by the current set-up.
Â
On-site Supervision
- Routine practices: Although monitoring routines are in place, they need to be improved.
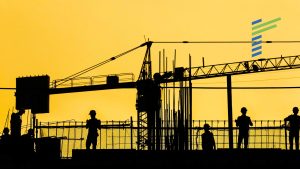
Workforce productivity peaks with clarified role definitions
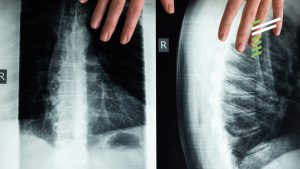
Vendor management saves healthcare centre $12 million
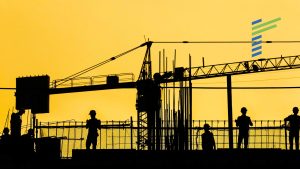
Workforce productivity peaks with clarified role definitions
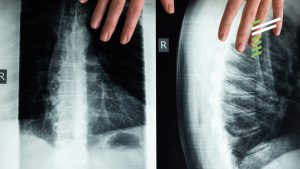
Vendor management saves healthcare centre $12 million
Ready for a change in your organisation?
Project Approach
This 10-month project was set up to design, develop, and implement sustainable solutions to address key challenges faced by company management. It began with a comprehensive analysis to identify the root causes of these issues.
The project was organised into four distinct work streams. Cross-functional teams led by department heads, were established. Weekly Management Action Team (MAT) meetings were held to facilitate communication, and monthly progress reports were submitted to the Central Steering Committee.
As solutions to long-standing problems emerged, the enthusiasm of the teams grew significantly. The teams became a driving force for positive change, united by a common goal: to achieve significant improvements in overall business performance through process and digital transformation.
ImplementationÂ
“The project exceeded my expectations in terms of process improvement, people development and financial benefit. While the financial benefit is great, I am most pleased with the staff development that will continue to pay dividends for years to come.”
 – Regional Vice President
Performance Management
To ensure successful delivery and track the impact of the overall effort, several key activities were implemented, including:
- Asset teams were realigned to prioritise leading indicators and manage Key Performance Indicators (KPIs) on an exception basis. This was facilitated by the Lever Metric Dashboard.
- Monthly performance meetings were redesigned.
- The integration of strategic activities was linked to weekly performance metrics, creating a “short-interval control” system that influenced daily performance, and led to improvements across all metrics.
- A digital meeting effectiveness dashboard was implemented to drive better meeting behaviour and structure for performance review meetings.
Â
Engineering Ways of Working
- The Engineering MAT implemented a Management Control System (MCS) to establish a transparent demand management process. This ensured that only prioritised work entered the system, resulting in a reduction of 12 full-time contractors.
- The team also developed and implemented Service Level Agreements (SLAs) to ensure a consistent and timely service levels for engineering customers.
- A Replacement-In-Kind (RKI) process was established, supported by a dedicated software tool that streamlines RKI requests and acts as a central communication channel for both supply chain and engineering approvals.
Â
Maintenance & Programme Execution (PE) and Offshore Ways of Working
- Introduced forward-looking metrics that identify total craft manpower capacity to enable the validation team to assign Basic Start Dates (BSDs) and Basic Finish Dates (BFDs) to CMOs with the highest potential for timely completion.
- To reduce and manage the backlog, each asset team received targeted training to equip them with the skills for long-term backlog management.
- A total of 138 low-value, unnecessary, or duplicate CMOs were cancelled, freeing resources for critical maintenance tasks.
- Over 30,000 maintenance manhours were removed from the backlog.
Â
Digital Tools
The use of the following digital tools was key to the success of this project:
- The use of Celonis for process mining to facilitate process mapping, analysis and improvement.
- A labour delivery tool was implemented to match labour resources to a prioritised list of pending projects.
- Microsoft Power BI was used to view performance, savings, meeting evaluations, behaviour change and project status.
- A Replacement-In-Kind (RIK) tool was developed and implemented by Renoir to allow supply chain and engineering to seamlessly communicate approved replacements for items that are no longer available.
- A lever metrics dashboard was developed and implemented by Renoir to visually communicate leading indicators to enable short interval controls and process compliance checks.
Results
Overdue RKI requests reduced by
75%
Reduced the number of replanned maintenance orders by
35%
Consistent corrective maintenance orders (MOs) of
72%
Safety for critical work conformance for three assets reached
100%
The project delivered clear financial benefits and its impact went beyond immediate cost savings. It fundamentally changed the way the functions worked, both individually and collaboratively.
Senior leaders benefited from a new governance structure that enabled deeper problem identification and resolution across the organisation. Individual contributors and those affected by process updates and new process development were involved in every step of the project.
Previously, the client had struggled to implement its recently adopted “Ways of Working” due to significant process gaps. The project’s focus on governance, collaboration, and digital transformation led to a step change in the organisation’s operational approach, resulting in faster problem resolution and improved financial performance.
By equipping the client with the necessary structure, tools, and skills, the project enabled them not only to understand and implement the new processes, but also to identify and close previously unseen gaps.
*We have intentionally omitted client-specific details to uphold strict confidentiality.  
Do you need help to change the way your organisation works and the behaviour of your people?