At a GlanceÂ
Rotating equipment management was proving a challenge for an LNG plant that was looking to improve its permit-to-work processes and reduce delays. After a 26-week project with Renoir, the following results were achieved:Â
- Implementation of new Management Control Systems in Turnaround, Permit-to-Work and Engineering Rotating EquipmentÂ
- No PTW-related incidents Â
- Improvement in PM:CM Ratio for Rotating Equipment Â
- Achievement of all critical schedule and quality milestones for the next major turnaroundÂ
BackgroundÂ
The client is an LNG plant in the Western Pacific with an ambitious joint venture between a national government in the region, as well as an oil & gas producer, and a top automobile manufacturer. Completed in the 1970s, its facility of over 100 hectares with more than 800 working personnel focuses on large scale liquefaction and transportation of natural gas which commands a sales volume of over 6 million tonnes of LNG annually. The company has established itself as one of the country’s major revenue earners and is expected to have a plant life until the year 2070.Â
The Challenge Â
Following from the success of the assignment to deliver improvements in maintenance execution, Renoir was engaged to continue the change program as a 26-week project focusing on Turnaround, Permit-to-Work (PTW) and Engineering Rotating Equipment (ERE). The key objectives were around improving the client’s safety management system and the reliability of major units and equipment in the plant. The goal was to eliminate PTW-related incidents, achieve zero days delay in Turnaround and improve the ratio of preventive maintenance to corrective maintenance (i.e. PM:CM Ratio) for rotating equipment.Â
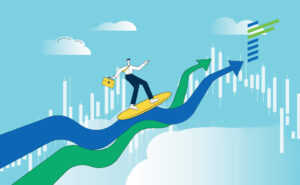
When sales structure improves, revenue follows
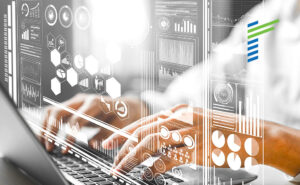
Part I: Digital delivery challenges in financial services
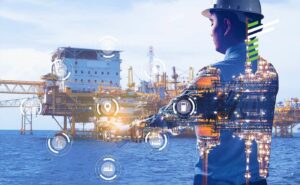
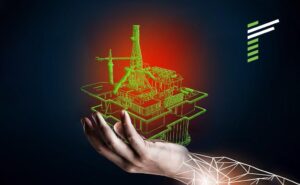
Rethinking Sales in Oil & Gas
Ready for a change in your organisation?
What We Did Â
The Project kicked off with Renoir’s Focus Process®, developed over many years, based on experiences with hundreds of successful assignments. Â
It ensured that consistent and sustainable outcomes were achieved. The process promoted commitment and ownership of the solutions being implemented, whilst retaining the company’s essential organisational goals and corporate identity. Â
To achieve maximum impact and buy-in, a “Management Action Team” (MAT) was set up, led by the client’s Business Improvement department, with direct involvement from Turnaround, ERE and PTW mangers to directly engage the respective departments and related interfaces in implementing the required improvements. A select team of client staff were seconded to the project as full-time task force, receiving training and working together with Renoir consultants to identify improvement opportunities, design the solutions, engage key stakeholders and drive behavioural change throughout the company.Â
Project Deliverables
Renoir, together with the client MATs, designed, developed and installed new Management Control Systems (MCS) and work processes in the Turnaround, ERE and PTW departments. The MCS for each workstream emphasised a holistic, proactive approach to Turnaround planning and coordination, PTW management, incident prevention, rotating equipment management and root cause analysis. Â
KPIs and the associated reporting mechanisms provided managers with constant feedback on the performance of their staff and equipment, while multiple feedback loops were installed at various stages of the process. This empowered managers to take effective actions and reduce performance gaps at appropriate levels and intervals.Â
Once the new ways of working were agreed upon by the client’s senior management, the project team set about driving behaviour change across the plant. Over 400 people (half of the plant) were directly impacted by the changes, and Renoir worked closely with all parties to provide training, coaching and day-to-day assistance. Â
The ResultsÂ
As a result of the changes in systems and behaviours, there were no PTW-related incidents in the plant for the entire six-month duration, while PM:CM Ratio for Rotating Equipment increased to 43:57. Meanwhile, preparation for the next major turnaround campaign has achieved 86% compliance to all scheduled milestones.Â
More significantly, the new Management Control System has allowed the client’s management to make informed decisions about strategies and plans, and has provided a stable platform for developing a culture of continuous improvement. It has also allowed for a smoother coordination of activities within client operations, thus ensuring that safety and reliability continue to be key focus areas for years to come.Â
“Renoir’s structured approach helped us a lot in achieving in our goals in Turnaround, managing work permits and preventive maintenance for rotating equipment. Besides achieving the results in these areas, our staff learned a lot from them on how to manage change in a structured way. Another job well done!”
– Client Deputy Managing Director
Leverage a Management Control System for improved coordination and compliance.