At a Glance
After a 50-week project with Renoir, the client had achieved the following:
- An overall 4-week running rate of well over a 100% improvement over base productivity, versus an initial target of 35%
- Concrete activities achieved were well over 130% improvement over base productivity against the same target
- Financial benefits exceeding QAR 40 million
Background
In June 2013, our client, as part of a joint venture, was awarded the design and construction of an underground metro line, scheduled for completion by 2019. The project involved the construction of over 30 km of tunnels, six underground stations and eight ancillary structures.Â
The Challenge
The client initiated a Renoir operational improvement project to optimise productivity and control direct manpower costs across its construction sites for the underground project. The overall aim was to generate significant savings from construction costs.
Renoir assembled a joint team consisting of consultants along with a client task force. A steering group of Renoir and client management was formed to oversee progress. Bi-weekly steering group meetings were held to ensure that the project remained on track and achieved the initial project plan. All changes and system elements involved the stakeholders to ensure a high level of ownership and sustainability.
Renoir also assembled Management Action Teams (MATs) whose role was to identify issues and root causes, assess impact, develop solutions and implement them. Extensive management and supervision training along with constant follow up, on-going coaching, and positive reinforcement continued throughout the entire duration of the engagement.
Through multiple diagnostic studies and observations, the joint team identified many of the root causes for low productivity; namely gaps in the management controls coupled with lack of appropriate key performance indicators at the execution level, ineffective operational planning and lack of quantitative real time progress measures.
What We Did
The project with Renoir ran for a period of 50 weeks and had the following key elements:
- Planning: A detailed planning process was provided by discipline that disseminated down to all levels via Supervisors and Foremen to the point of execution. This provided a set of clear daily tracked deliverables, and therefore resulted in more productive work areas.
- Resource Planning: A process for accurately assessing manpower requirements and a requisition process based on realistic and quantified work volume forecasts were provided.
- Active Supervision: By working closely with foremen, supervisors and engineers, supervisory practices were monitored and improved through training and coaching. Protocols based on Active Management Behaviour techniques were implemented to drive a more productive work site.
- Target Rates: Relevant and accurate production rates were formulated and implemented, along with measurement of performance against those rates to relate directly to the enhanced level of active supervision and targets. In turn, this provided valuable feedback to operational planning and higher level forecasting and project budgeting. Additionally, stretch targets well above the base production rates were developed, agreed on and implemented.
- Improved coordination and communication: Better communication between different areas resulted in better alignment with construction priorities. Scarce resources, material, equipment and skills were optimised, leading to increased operational efficiency and optimum alignment.
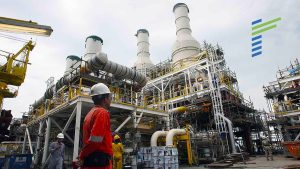
Oil & Gas Plant Optimizes Tool Time & Planning Efficiency

How a construction JV achieves a 30% improvement in productivity
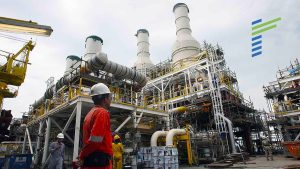
Oil & Gas Plant Optimizes Tool Time & Planning Efficiency

How a construction JV achieves a 30% improvement in productivity
Incentivise high performance with a Management Control System
Another critical step was implementing a daily measurement system of work completed by each supervisor. The Time & Quantity Report was developed and implemented which the foreman and engineer utilised to quantify the work completed along with the number of man-hours used. This allowed detailed definition of activities, the setting of a baseline, tracking of progress and objectively assessing the results of interventions.
One of the important features of the assignment was the development and implementation of dashboards to provide visibility of production indicators at all sites. An overall all-stations dashboard showed key performance indicators for the sites and these were reviewed centrally with all station managers, whilst station-based dashboards showed detailed key performance indicators that were reviewed at the station level.
A recognition process for over-achieving foremen that fostered competition and enthusiasm was implemented. Weekly and monthly Foreman League Tables were produced and publicised across all sites to incentivise high achievements and performance.
Results
The target was an estimated improvement in direct labour productivity of at least 35% within the time frame of the project. Due to the great collaboration between the client and Renoir, the project achieved an increase in labour productivity of more than 100%, which resulted in considerable savings (against the baseline performance levels) for the client.
“The level of details required in the daily reporting and weekly planning helped our people take responsibility and pay attention to the performance that was not there before.”
Stations Manager
Publicise achievements for enhanced performance at the work site.